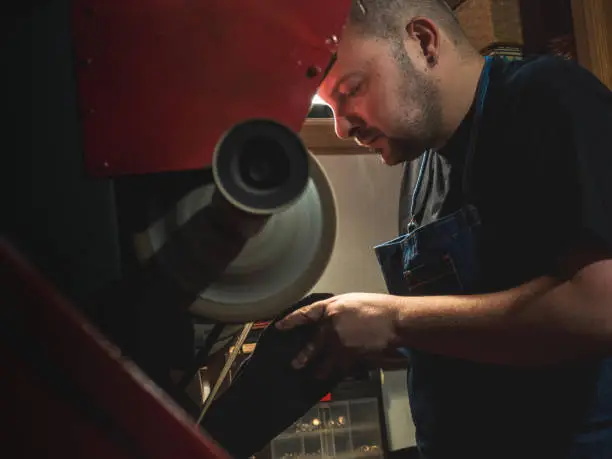

The benefits of prototype development in metal spinning
Metal spinning is a versatile and cost-effective manufacturing process that offers numerous benefits to a wide range of industries. Prototype development plays a crucial role in enhancing the efficiency and effectiveness of metal spinning, ultimately leading to improved product quality, reduced costs, and increased customer satisfaction. In this article, we will explore the various advantages of prototype development in metal spinning and how it is shaping the future of this innovative manufacturing technique.
The basic principles of metal spinning
At its core, metal spinning involves securing a metal blank onto a spinning lathe, which is then rotated at high speeds. The spinning action, combined with the application of pressure using specialised tools, causes the metal to flow and take on the shape of the spinning mould or mandrel. The process is highly customisable, allowing manufacturers to create intricate designs and achieve precise tolerances. Metal spinning offers several benefits over other traditional manufacturing processes, including cost-effectiveness, versatility, and the ability to produce complex shapes with high precision.
The role of technology in modern metal spinning
Advances in technology have significantly enhanced the metal spinning process. Computer Numerical Control (CNC) machines have revolutionised metal spinning by enabling the automation of the process, resulting in increased efficiency, accuracy, and reproducibility. CNC metal spinning machines allow manufacturers to program complex spinning sequences, reducing the risk of errors and enhancing overall productivity.
Furthermore, the use of CAD/CAM software has further streamlined the metal spinning process. With CAD/CAM, designers can create detailed 3D models of the desired shape, which can then be translated into machine-readable code for CNC machines to follow. This eliminates the need for manual measurements and calculations, reducing the chances of human error and ensuring consistent results.
In addition to technology, the skill and expertise of metal spinners play a crucial role in the success of the process. Experienced spinners understand the nuances of different metals and their behaviour during spinning, allowing them to make precise adjustments to achieve the desired shape and finish. They also possess a deep understanding of the limitations and capabilities of the spinning machines, enabling them to optimise the process for maximum efficiency and quality.
The importance of prototype manufacturing and development
In the context of metal spinning, prototyping involves creating a preliminary version of the desired product using the same materials and production processes as the final product. This allows manufacturers to assess its functionality, fit, and finish, and make any necessary adjustments early in the design process. Prototyping also enables designers and engineers to collaborate closely, resulting in improved communication and a better understanding of design requirements.
Prototype development plays a crucial role in the success of any manufacturing process, and metal spinning is no exception. Prototyping allows manufacturers to test and refine their designs, identify potential issues, and make necessary modifications before full-scale production. This iterative approach reduces the risk of costly errors and ensures that the final product meets the desired specifications.
If you’re looking for guidance on how to submit initial prototype designs to metal spinners, read ‘What to know when supplying a drawing for metal spinning’.
Benefits of prototyping in metal spinning
Firstly, it provides a realistic representation of the final product, allowing manufacturers to evaluate its performance and functionality. This helps in identifying potential design flaws, optimising the manufacturing process, and minimising material waste. Additionally, prototyping enables manufacturers to assess the feasibility of mass production, allowing for efficient scaling up of production once the prototype is approved.
Furthermore, prototype development in metal spinning allows manufacturers to test the product’s durability and reliability. By subjecting the prototype to rigorous testing, manufacturers can identify any weak points or areas that require reinforcement. This ensures that the final product will withstand the demands of its intended use, providing customers with a high-quality and long-lasting solution.
Another significant benefit of prototype development is the opportunity it provides for cost-saving. By identifying and resolving design issues during the prototyping phase, manufacturers can avoid expensive modifications or recalls once the product is in full-scale production. This not only saves money but also reduces the time-to-market, allowing manufacturers to meet customer demands more efficiently.
How prototyping can save costs
By catching design or production issues early in the prototyping stage, manufacturers can avoid costly mistakes that could impact the bottom line. Rectifying these issues during full-scale production would not only be more expensive but also result in product delays, customer dissatisfaction, and potentially damage to the company’s reputation. Prototyping minimises these risks and ensures a smooth transition from design to production.
Furthermore, prototyping allows manufacturers to optimise the material utilisation and production processes, leading to cost savings in the long run. By identifying and rectifying any inefficiencies or waste during the prototyping stage, manufacturers can implement improvements and achieve higher productivity and reduced material scrap during full-scale production.
Moreover, prototyping fosters innovation and creativity within the manufacturing industry. It encourages experimentation with new materials, techniques, and designs, pushing the boundaries of what is possible in metal spinning. This spirit of innovation not only drives cost savings but also positions companies at the forefront of technological advancements, giving them a competitive edge in the market.
The future of prototype development in metal spinning
The world of metal spinning is constantly evolving, and prototype development will continue to play a pivotal role in shaping its future. Emerging technologies, such as additive manufacturing and advanced simulation techniques, are making prototyping even more efficient and cost-effective.
Metal spinning, a traditional manufacturing technique dating back centuries, has seen a resurgence in recent years due to its versatility and ability to create complex shapes with ease. The craft of metal spinning involves rotating a metal disc on a lathe while shaping it into a desired form using specialised tools. This method allows for the production of a wide range of products, from decorative items to precision components for aerospace and automotive industries.
Conclusion
In conclusion, prototype development plays a crucial role in the success of metal spinning. By allowing manufacturers to test and refine their designs, prototype development enhances product quality, reduces costs, and drives innovation. The iterative nature of prototyping ensures that the final product meets customer requirements and exceeds expectations. As technology continues to evolve, the future of prototype development in metal spinning looks promising, with emerging trends enabling even greater efficiency, cost savings, and creative possibilities.
Need an expert in prototype manufacturing?
Tanfield Metal Spinners are equipped with a vast tooling range, granting us the capabilities to take on almost any metal spinning project. By utilising our precision metal spinning services, we can create prototypes by following unique designs that meet exact specifications. Get in touch if you have any questions about how we use prototypes in our metal spinning services.